Realization of Environmentally-friendly Electrochemical Machining with Ultra-low concentration electrolyte and Suction Tool
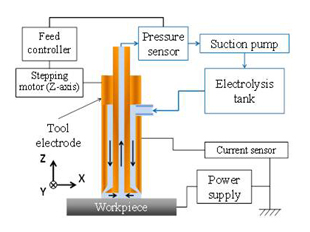
Research members: Dr. Wataru NATSU
Research fields: Mechanical engineering
Departments: Division of Advanced Mechanical Systems Engineering, Institute of Engineering
Keywords: Manufacturing, Machining, Non-traditional machining, ECM, EDM, Polishing
Web site:
Summary
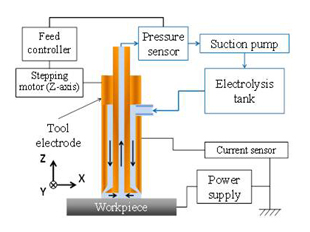
Electrochemical machining (ECM) technology is widely applied in machining hard-to-cut metallic materials regardless of their hardness. However, the machining accuracy is lower comparing with that in EDM, because machining takes place not only beneath the tool electrode but also around the surrounding area. Also, the acid and alkaline electrolytes used in machining are dangerous to the operators and cause environmental problems. In order to solve these problems and broaden the ECM application, utilizing ultra-low concentration electrolyte and the suction tool were proposed.
1. ECM with ultra-low concentration electrolyte
This study creatively uses the common mineral water as the electrolyte for ECMM and preliminarily performs the experiments to confirm its machining capability in ECMM. The obvious advantage by using the mineral water as the electrolyte can be concluded in the aspect of environment, economy, and system control, etc. It will be promising for the mineral water to be used in the production of MEMS, such as micro pin by the method of ECMM, for it is totally eco-friendly, no pollution, low cost, high efficiency and no corrosion and wear of the machine tool. During the fabrication of the micro pin, high voltage power supply is essential through experimental observation, which is different from traditional ECM. And the micro WC pin in the diameter of 20 to 30 μm is obtained from a 300 μm diameter WC pin in about 10 minutes in this study. Furthermore, in this study, the machining property and potential of the mineral water as the electrolyte are investigated to find out that its response to the ultra-short pulsed power supply is much faster than conventional electrolyte, like NaNO3 and more suitable for the cases using nano-second pulse power supply, in other words, in the micro-ECM.
2. ECM with suction tool
The tool structure and the machining system are shown in Fig.1. When the tool electrode approaches the workpiece, sectional area of the flow channel becomes narrower. In the narrower flow channel, the air flows faster between the tool electrode and workpiece. This makes the pressure lower in the area between the tool and workpiece. Therefore, the electrolyte is suctioned from the aperture, and starts to circulate. No electrolyte flows towards the outer periphery with this method. Also, the gap-width detection and control is realized through monitoring the suction pressure, since the pressure changes with the gap-width. To confirm the above principle, the machining experiments were carried out by drilling a blind hole and generating a complicated shape with the proposed tool electrode and the feed controlling system. As the result, the effectiveness of electrolyte confinement and gap-width detection, also the possibility of shape generation were verified through simulations and experiments.
Reference articles and patents
1) Ye Yang, Wataru Natsu, Wensheng Zhao: "Realization of eco-friendly electrochemical micro-machining by using mineral water as the electrolyte", Precision Engineering, 35(2), 204-213, 2011
2) Wataru Natsu, Hisashi Nakayama, Zuyuan Yu: "Improvement of ECM Characteristics by Applying Ultrasonic Vibration", International Journal of Precision Engineering and Manufacturing, 13(7), 1131-1136, 2012
3) Naoki Shibuya, Yukihiro Ito, Wataru Natsu: "Electrochemical Machining of Tungsten Carbide Alloy Micro-pin with NaNO3 Solution", International Journal of Precision Engineering and Manufacturing, 13(11), 2075-2078, 2012
4) Katsuaki Endo, Wataru Natsu: "Proposal and Verification of Electrolyte Suction Tool with Function of Gap-width Detection", International Journal of Electrical Machining, 19, 34-39, 2014
5) Dahai Mi, Wataru Natsu: "Proposal of ECM Method for Holes with Complex Internal Features by Controlling Conductive Area Ratio along Tool Electrode", Precision Engineering, 2015 (accepted)
Contact
University Research Administration Center(URAC),
Tokyo University of Agriculture andTechnology
urac[at]ml.tuat.ac.jp
(Please replace [at] with @.)